Demand Control Ventilation
New CommercialWhat is Demand Control Ventilation?
Ventilation systems in commercial buildings, whether passive or active, help maintain the proper mix of gases in the air, control odors, and exhaust contaminants from occupied spaces (see Natural Ventilation, Properly Sized HVAC Equipment). Ventilation systems typically provide a constant flow of fresh air to occupants based on maximum building occupancy or full ventilation rates in contrast to a minimum or area ventilation rate based on reduced occupancy levels. Demand control ventilation (DCV) modulates between full and area ventilation rates based on actual or estimated occupancy levels, saving energy and improving indoor air quality. DCV systems can measure occupancy levels and adjust ventilation using one or more of the following methods:[1]
- Carbon dioxide (CO2) sensors that adjust airflow based on CO2 levels or the number of occupants in a space.
- Occupant counting which counts actual or estimated occupants in a space using ticket sales, security swipes or video monitoring.
- Occupancy sensors that detect occupancy and switch between full or area ventilation rates.
- Scheduled ventilation based on estimated and scheduled occupancy.
- Set supply air CO2 concentrations based on design occupancy conditions in designated zones.
Figure 1 compares the different DCV methods and corresponding ventilation rates in response to changing occupancy levels.
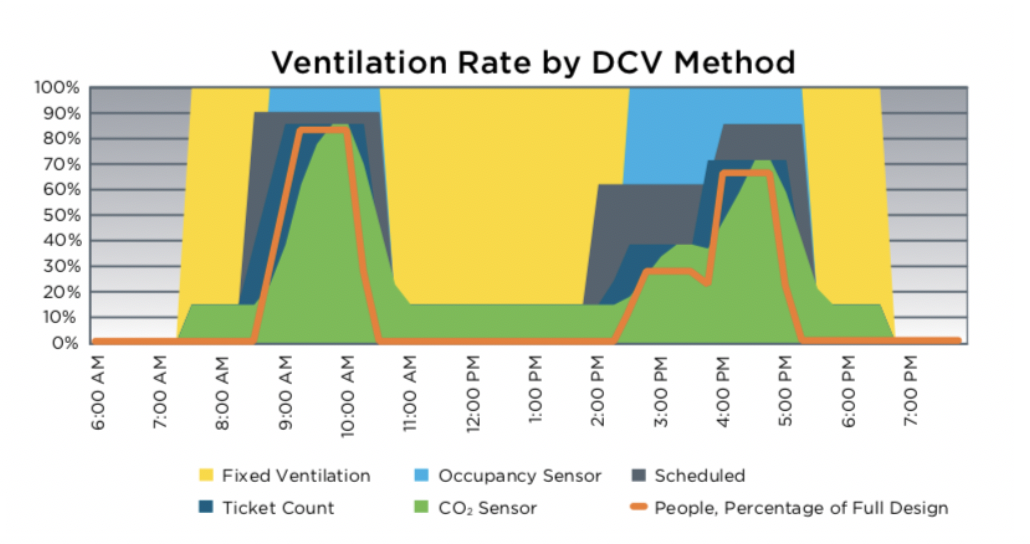
Fig 1. Ventilation rates provided with fixed ventilation and DCV alternatives (Source: US DOE: Building Energy Codes)
How to Implement Demand Control Ventilation
Proper ventilation and good indoor air quality start with eliminating or reducing familiar sources of indoor air pollution such as off-gassing from building materials and furnishings.
When designing a new DCV system, best practices include using zone occupancy sensors for small and less densely occupied zones, and CO2 sensors in large or densely occupied spaces, both with setpoints that follow the specific guidelines in Appendix A of the ASHRAE Standard 62.1 User’s Manual.[2] Well-designed and executed DCV systems take into account user requirements, operator training, and coordination among different building systems, such as occupancy sensors used for lighting and air flow. Commissioning and recommissioning provides an opportunity to check DCV set-points and offer potential energy and cost savings.
Examples
Information on a subset of six building systems collected from 32 buildings was taken across all seasons using building automation system data and instrumentation to document energy savings and indoor air quality before and after recommissioning of Demand Control Ventilation (DCV) systems. Building occupants also completed a comfort survey. System designers and operators provided lessons learned. Results showed that DCV implemented in large VAV systems can provide significant energy and cost savings in cold climates and recommissioning either provides additional energy savings or increased indoor air quality.[3]
Oradell Public School, Oradell, NJ
The Oradell Public School conducted an energy audit as part of the New Jersey Board of Public Utilities’ Local Government Energy Audit Program. The report recommended Demand Control Ventilation (DCV) as an Energy Conservation Measure (ECM) to reduce energy and utility costs and to improve indoor air quality. The following summarizes the estimated implementation costs and savings for Demand Control Ventilation (DCV):
- Electricity Savings: 18,400
- Natural Gas Savings: 2,700
- Estimated Savings: $5,200
- Estimated Installed Cost: $10,000
- Payback Period: 1.9
Benefits
Ventilation requires energy to heat or cool outside air. Demand control ventilation (DCV) saves energy by reducing ventilation rates during times of vacancy and reduced peak occupancy. DCV improves indoor air quality, contributing to occupant health and productivity, by closely monitoring CO2 concentrations and occupancy levels that impact indoor air pollution and air quality.
Costs
Compared to conventional ventilation systems, demand control ventilation adds up-front costs depending on the complexity and size of the system and number of sensors installed, ranging between $1 – $3 per cfm of outside air.[4]
Resiliency
Demand control ventilation (DCV) offers an indirect resiliency benefit to buildings by reducing heating and cooling loads, thereby reducing stress on the grid, and the likelihood of brownouts.
[1] U.S. DOE. “Demand-Controlled Ventilation.” https://www.energycodes.gov/sites/default/files/documents/cn_demand_control_ventilation.pdf (accessed May 31, 2018).
[2] SeventhWave. 2015. Energy Savings from Implementing and Commissioning Demand Control Ventilation: Lessons learned from observed practical approaches. Prepared for Minnesota Department of Commerce – Division of Energy Resources.https://www.seventhwave.org/sites/default/files/276-1_0.pdf (accessed Nov 19, 2018).
[3] SeventhWave. 2015. Energy Savings from Implementing and Commissioning Demand Control Ventilation: Lessons learned from observed practical approaches. Prepared for Minnesota Department of Commerce – Division of Energy Resources. https://www.seventhwave.org/sites/default/files/276-1_0.pdf (accessed Nov 19, 2018).
[4] SeventhWave. 2015. Energy Savings from Implementing and Commissioning Demand Control Ventilation: Lessons learned from observed practical approaches. Prepared for Minnesota Department of Commerce – Division of Energy Resources.https://www.seventhwave.org/sites/default/files/276-1_0.pdf (accessed Nov 19, 2018).