Variable Frequency Drives
Existing CommercialWhat is a Variable Frequency Drive (VFD)?
A variable frequency drive (VFD), also known as a variable-speed drive, adjustable-speed drive or inverter refers to a device that controls the voltage and frequency supplied to a motor, varying the speed of a motor or the flow in distribution systems.[1] Flow can refer to various systems such as water, air or energy. Many applications and existing commercial HVAC systems use fixed or single speed motors and regulate flow and pressure with dampers and valves, which can throttle and reduce efficiency.[2]
VFDs on fans (e.g., supply and return fans, exhaust fans, boiler fans, or condenser fans) save energy by allowing the volume of air moved to match the system demand. VFDs can control the speed of electric motors by applying a low frequency and a low voltage during motor startup, then ramping up to accelerate the load while limiting current. During a shutdown, VFDs can also allow motors to ramp down at a controlled rate. [3] When applied to a HVAC system, more specifically the air handling units (AHU), VFDs can vary motor speed to precisely match the load, a critical energy-saving measure for frequently oversized HVAC systems that work inefficiently at part-load (see Part-Load Efficiency and Properly-Sized HVAC Equipment).[4]
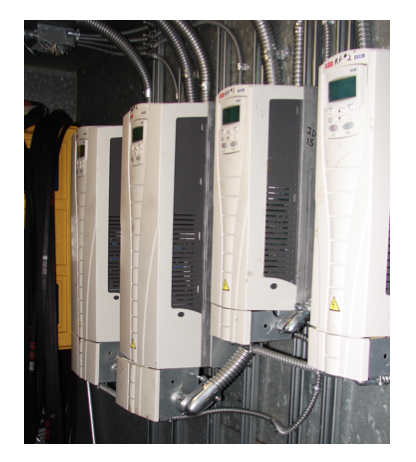
Figure 1 – Variable frequency drives, Atrium Building – Secaucus, NJ (Source: Rutgers Center for Green Building)
How to Incorporate Variable Frequency Drives
Coordinate work between the mechanical engineer and contractor to determine opportunities to install VFDs and to size VFDs to match load requirements accurately. In general, existing systems with constant speed motors that already modulate flow with mechanical devices provide a better match for VFD retrofits than existing systems that require constant flow.[5]
Example
Rutgers University Campuses, New Brunswick, Newark and Camden, NJ.
University engineers at Rutgers conducted a comprehensive energy audit and identified the opportunity to save energy and costs by installing premium efficiency motors and variable frequency drives at multiple campus buildings spanning several university locations. The project expects to have a three-year payback and save an average of 2.8 million kilowatt hours of electricity and prevent the release of 1,500 tons of CO2 on an annual basis.[6] VFDs can also contribute to demand reduction under the right operational scenario.
Benefits
- Minimizes mechanical and electrical stress on the motor system, lowering maintenance and repair costs and extending motor life.[7]
- Reduces the horsepower (HP) required to run a system by the cube of its motor speed, providing significant energy, demand and costs savings when motor speeds can vary to match a load.[8]
- Enhances overall system performance by matching system capacity to the actual load.
- Allows for improvements in thermal comfort which can impact occupant satisfaction and productivity.
Costs
The cost of incorporating VFDs into an existing HVAC system depends on the characteristics of the existing system and on the manufacturer and supplier. Equipment costs also vary depending on the horsepower (HP) rating, ranging from $1,000 for 5 HP VFD models to $15,000 for 200 HP VFD models.[9] Energy savings from reduced maintenance and longer equipment life and available incentives can reduce payback periods and increase long-term savings.
Check the New Jersey Office of Clean Energy for available incentives.
Resiliency
VFDs increase resiliency by decreasing energy and water consumption, and peak loads which decreases reliance and stress on the electricity grid and natural gas and water and wastewater infrastructure.
[1] Bernier, Michael A, and Bernard Bourret. 1999. Pumping energy and variable frequency drives. ASHRAE Journal. 37.
[2] Centre for Energy Advancement through Technological Innovation (CEATI) International. 2009. Variable Frequency Drives: Energy Efficiency Reference Guide. https://www.ceati.com/freepublications/7025_guide_web.pdf (accessed Dec 7, 2018)
[3]Yaskawa. “Five Reasons for VFDs in HVAC Applications.” https://www.yaskawa.com/delegate/getAttachment?documentId=WP.HVAC.03&cmd=documents&documentName=WP.HVAC.03.pdf (accessed June 4, 2018).
[4] Whole Building Design Guide. 2016. High-Performance HVAC. National Institute of Building Science. https://www.wbdg.org/resources/high-performance-hvac (accessed Nov 28, 2018).
[5] Edward Sullivan. 2014. “Analyze VFD (Variable Frequency Drive) Retrofit Applications To Ensure Savings.” FacilitiesNet https://www.facilitiesnet.com/hvac/article/Analyze-VFD-Variable-Frequency-Drive-Retrofit-Applications-To-Ensure-Savings–14674 (accessed Dec 5, 2018).
[6] Project information, savings and environmental benefits provided by Michael Kornitas, Energy Conservation Manager, Rutgers University.
[7] California Energy Commission. “Water/Wastewater Efficiency: Variable frequency drives.” http://www.energy.ca.gov/process/pubs/vfds.pdf (accessed June 4, 2018).
[8] American Society for Healthcare Engineering (ASHE). 2010. Sustainability Roadmap: Install Variable Frequency Drives on Pumps and Motors. http://www.sustainabilityroadmap.org/pims/224#.XAgk9C3Mzq0 (accessed Dec 7, 2018).
[9] Navigant. 2013. “Incremental Cost Study Phase Two Final Report – A Report on 12 Energy Efficiency Measures Incremental Costs in Six Northeast and Mid-Atlantic Markets. Prepared for the Evaluation, Measurement and Verification Forum. Chaired by the Northeast Energy Efficiency Partnerships. https://neep.org/sites/default/files/resources/NEEP%20ICS2%20FINAL%20REPORT%202013Feb11-Website.pdf (accessed Dec 19, 2018).