Exterior Wall Systems
Existing CommercialWhat is Upgrading Exterior Wall Systems?
Conditions that may lead to an upgrade of an exterior wall system include but are not limited to: water damage, mold, inadequate insulation, holes, cracks or other fractures that compromise structural integrity. Upgrading exterior walls provides the opportunity to fix structural or cosmetic damages, control moisture, improve insulation, and increase daylighting. Common wall system upgrades include:
- Adding insulation
- Air sealing doors and windows
- Repairing holes, cracks and gaps
- Upgrading windows and glazing
The building envelope or the physical structure between the inside of the building and the outside environment includes walls, windows, doors, roof systems, and the foundation.[1] Exterior wall systems often comprise the majority of the building envelope, playing a pivotal role in determining levels of comfort, natural lighting and ventilation, and the energy required to heat and cool a building.[2]
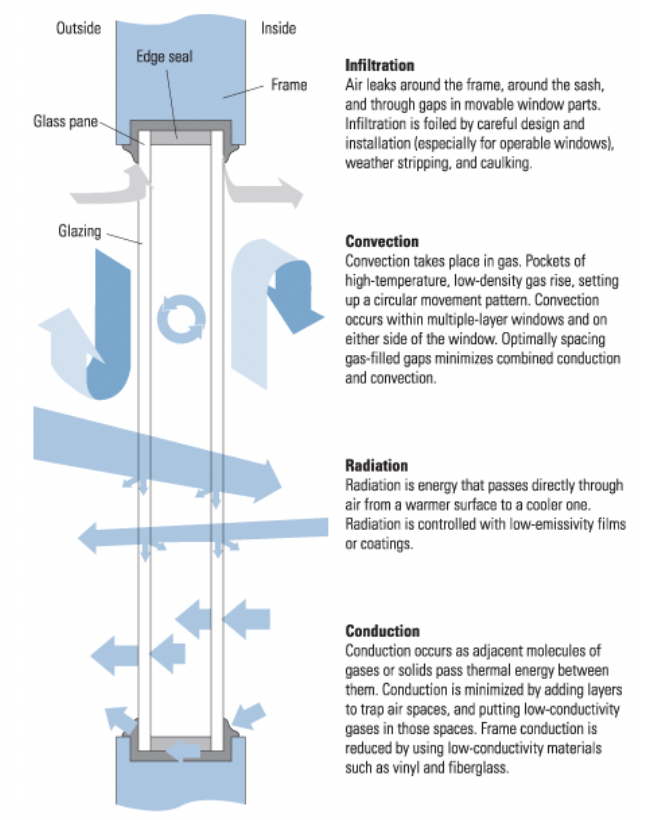
Figure 1 – Window energy flows (Source: ENERGY STAR)
Building R-values assess a wall’s thermal resistance. The higher the R-value, the better the building in reducing heat loss.[3] Air leakage contributes to 25- 40% of a building’s heat loss (see Air Infiltration).[4] Maintaining and investing in well-insulated (high R-value rating) walls/wall systems yields energy savings.
The following includes examples of insulation materials and wall systems:[5]
- Continuous and Cavity Insulation. Continuous insulation runs uninterrupted over structural membranes, avoids thermal bridging and is installed on the exterior surface of the building envelope.[6] Cavity insulation is installed between structural components such as wood studs.
- Composite Metal Panels consist of two sheets of metal adhered to a core material and include:[7]
- Foamed-Insulation Core Metal Wall Panels
- Laminated-Insulation Core Metal Wall Panels
- Honeycomb Core Metal Wall Panels
- Exterior Insulation Finish Systems (EIFs) consists of exterior wall cladding made of rigid insulation boards. The polymer-based (PB) system is most popular and consists of closed expanded polystyrene (EPS) insulation finished with a polymeric (organic) bonded aggregate and cement reinforced with a glass mesh.[8] Being lightweight and low cost, and the ability to achieve different aesthetic effects make EIFs a popular choice.[9]
- Insulated Concrete Forms (ICFs) consists of concrete walls poured inside foam insulation forms with steel reinforcing and stacked as interlocking blocks.[10] Insulated concrete block or concrete masonry units (CMUs) form prefabricated blocks applied like traditional block wall construction.
- Structural Insulated Panels (SIPs) consist of an insulating foam core placed between two structural panels, typically oriented strand board (OSB) or fiber cement panels.[11]
- Vacuum Insulated Panels (VIPs) consist of an interior, solid layer of a high R-value material wrapped in an exterior layer of airtight foil with a vacuum drawn inside the airtight foil.[12] They can achieve an R-value of 50 without adding bulk, making them cost-effective on roofs.[13]
How to Upgrade Exterior Wall Systems
Assess the building’s existing insulation and daylighting levels. Consider hiring a building envelope contractor experienced in air sealing and insulation. Perform an energy audit including a blower door test to measures the airtightness of the building and identify problem areas. Hire a daylighting professional to identify cost-effective opportunities to improve daylighting (see Daylighting and Windows and Skylights).
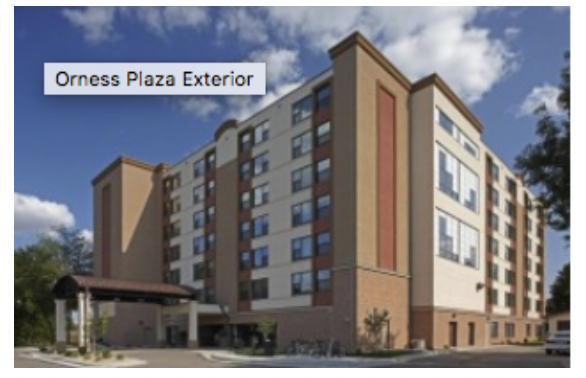
Figure 2. EIFs and metal panel assembly with an R-value of 16 and continuous insulation. (Source: US DOE Better Buildings Solution Center)
The US DOE recommends reducing envelope leakage and minimizing air infiltration by sealing, caulking and placing weather-strip to the following areas:[14]
- Joints around fenestration and door frames.
- Junctions between walls and foundations, between walls at building corners, between walls and structural floors or roofs, and between walls and roof or wall panels.
- Openings at penetrations of utility services through roofs, walls, and floors.
- Site-built fenestration and doors.
- Building assemblies used as ducts or plenums.
- Joints, seams, and penetrations of vapor retarders.
- All other openings in the building envelope.
Re-caulking and weather stripping windows and doors provide a low-cost option for upgrading the exterior wall system by minimizing air leakage. Poorly sealed buildings lack humidity control, contributing to moisture damage and mold growth that damages building materials and impacts the structural integrity of the building. Airtight buildings improve the effectiveness of insulation. Balancing airtightness with controlled ventilation helps to supply the appropriate level of fresh air into the building.
Example
Passive House Institute, US strategies applicable to commercial building retrofits, include:
- A combination of internal and external insulation to reduce thermal bridging
- Whole building air barriers, with commissioning before occupancy
- Moisture management in enclosure assemblies
- “Cool walls” that have optimum reflectivity and ventilation against solar gain
Benefits
A properly designed exterior wall system offers the following benefits.[15]
- Reduces energy costs
- Prevents moisture condensation
- Reduces capacity and size of new mechanical equipment
- Reduces noise levels
- Increases indoor environmental quality and thermal comfort.[16]
- Provides fire protection
Costs
The cost of adding insulation, air sealing doors and windows, and filling gaps and holes vary based on the conditions and scope of the project. There are often incentives available for upgrading exterior wall systems. See the New Jersey Office of Clean Energyfor available incentives and financing programs.
Resiliency
Expertly designed and installed exterior wall systems offer several essential resiliency benefits. In the event of a power outage, well-insulated buildings protect against heat loss in the winter and heat gain in the summer, helping to maintain comfortable internal temperatures for building occupants, and reducing stress on the grid. A daylighting-optimized building continues to provide interior light to building occupants when the power goes out. Wall assembly systems (with insulating properties) such as precast concrete panels, insulated concrete forms (ICFs), and structural insulated panels (SIPs) offer resistance to hazards such as fire, wind, earthquakes, and floods, and improve indoor environmental quality through resistance to mold.[17]
[1] Arnold, Chris. 2016. “Building Envelop Design Guide.” Whole Building Design Guide (WBDG). National Institute of Building Sciences (NIBS). https://www.wbdg.org/guides-specifications/building-envelope-design-guide/building-envelope-design-guide-introduction (accessed May 29, 2018).
[2] Vivian Loftness et al. (2012) State of the Art in Enclosure Technologies and Integrated Systems for 50% Energy Savings in Existing Commercial Buildings. Consortium for Building Energy Innovation. http://cbei.psu.edu/wp-content/uploads/2016/07/State-of-the-Art-in-Enclosure-Technologies.pdf (accessed June 4, 2018).
[3] US DOE | Energy Savers: Insulation. https://www.energy.gov/energysaver/weatherize/insulation (accessed May 31, 2018).
[4] US EPA Energy Star. Reduce Air Infiltration. https://www.energystar.gov/index.cfm?c=new_homes_features.hm_f_reduced_air_infiltration (accessed May 31, 2018).
[5] US DOE: Better Building Solution Center. Building Envelope Webinars for Walls
https://betterbuildingssolutioncenter.energy.gov/toolkits/building-envelope-webinars-walls (accessed May 29, 2018).
[6] US DOE Building Energy Codes Resource Center. “Cavity and Continuous Insulation.”
https://www.energycodes.gov/sites/default/files/documents/ta_cavity_and_continuous_insulation_in_rescheck.pdf (accessed May 29, 2018).
[7] Zwayer, Gary L. 2016 “Exterior Insulation and Finish Systems (EIFs).” Whole Building Design Guide. National Institute of Building Sciences.https://www.wbdg.org/guides-specifications/building-envelope-design-guide/wall-systems/exterior-insulation-and-finish-system-eifs (accessed May 29, 2018).
[8] Lstiburek, Joseph. 2007. “EIFs: Problems and Solutions.” Building Science Corporation. https://buildingscience.com/documents/digests/bsd-146-eifs-problems-and-solutions (accessed May 29, 2018).
[9] Zwayer, Gary L. 2016. “Exterior Insulation and Finish Systems (EIFs).” Whole Building Design Guide. National Institute of Building Sciences.https://www.wbdg.org/guides-specifications/building-envelope-design-guide/wall-systems/exterior-insulation-and-finish-system-eifs (accessed May 29, 2018).
[10] US DOE: Building America Solution Center: ICFs. https://basc.pnnl.gov/resource-guides/insulated-concrete-forms-icfs#quicktabs-guides=1 (accessed May 29, 2018).
[11] Structural Insulated Panel Association (SIPA). “What are SIPS?” https://www.sips.org/about/what-are-sips (accessed May 29, 2018).
[12] Dan Howell et al. “Vacuum Insulated Panels (VIPs) in a roofing application of US Post Office and Courthouse Camden, NJ.” March 2014. ORNL https://www.gsa.gov/cdnstatic/GPG_Vacuum_Insulated_Panels_03-2014.pdf (accessed May 29, 2018).
[13] GSA. Green Proving Ground Program. “Vacuum Insulated Panels in Roofing Applications.” March 2016. https://www.gsa.gov/governmentwide-initiatives/sustainability/emerging-technologies/published-findings/building-envelope/vacuum-insulated-panels(accessed May 29, 2018).
[14] US DOE Advanced Energy Retrofit Guides. https://www.energy.gov/eere/buildings/advanced-energy-retrofit-guides(accessed May 31, 2018).
[15] National Insulation Association. Benefits of Insulation. https://insulation.org/about-insulation/benefits-of-insulation/ (accessed May 29, 2018).
[16] Whole Building Design Guide. “HVAC Integration of the Building Envelope.” http://wbdg.org/guides-specifications/building-envelope-design-guide/building-envelope-design-guide-introduction (accessed May 29, 2018).
[17] New Jersey Climate Adaptation Alliance (NJCAA). 2014. The Role of Buildings in Climate Adaptation. Climate Change Preparedness in New Jersey. Page 11. Edited by Jennifer Senick. https://njadapt.rutgers.edu/docman-lister/resource-pdfs/111-green-bulding/file (accessed May 7, 2018).
Related Strategies
Resources
- Air Barrier Association of America
- Continuous Insulation
- Insulation Institute
- Metal Building Manufacturers Association
- North American Insulation Manufacturers Association (NAIMA)
- NJ Clean Energy Program
- Passive House Institute US
- Philadelphia High-Performance Building Renovation Guidelines – Guide 3
- Penn State Consortium for Building Energy Innovation
- Structural Insulated Panel Association
- Whole Building Design Guide – Envelope
US DOE